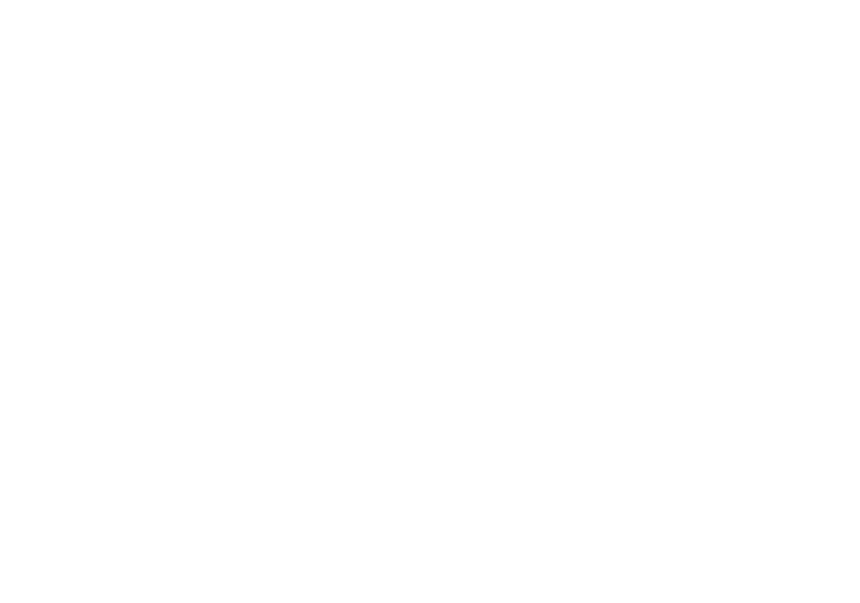
A connected supply chain accelerates decision-making at Godiva Japan
Supply planning and S&OP with Anaplan save hundreds of hours annually, with more benefits to come
Godiva Japan supplies gourmet chocolates to loyal customers in the East Asian country. After establishing a network of retail shops, the company expanded into supermarkets, convenience stores, and e-commerce, which complicated supply planning. By implementing Anaplan and integrating the platform with its ERP system, Godiva Japan can now collect and analyze sales and inventory data in a timely manner and quickly produce S&OP reports. Anaplan has reduced data analysis and reporting workloads and established a foundation for accurate demand planning.
We have sped up decision-making about supply planning with Anaplan, helping us prevent lost sales opportunities and excess stock.
300
fewer hours spent annually on monthly S&OP reporting accelerates decision-making
1,400+
hours saved annually on secondary data processing for S&OP eliminates manual data efforts
Instant
retained stock reports, which formerly required three people to work a full day, keep inventory fresh and balanced
Since opening its first shop in Japan in 1972, Godiva Chocolates has grown to about 330 stores, cafés, and ateliers throughout the country. The company has also expanded its reach into supermarkets, convenience stores, and e-commerce, and these diverse outlets supported solid growth, even through the COVID-19 pandemic. Godiva Japan's ongoing goal is to bring the feeling of “Elevating My Everyday” to its customers.
Master data on the company’s 10,000 different products, some of which are imported from Belgium and others that are produced locally, is recorded in an enterprise resource planning (ERP) system. But the data required for analyzing inventories and sales consisted of thousands of rows in multiple spreadsheets prepared by people dispersed throughout the company. This distributed data made supply chain management a challenge.
Overseeing the entire supply chain
When Godiva’s Japanese business became an independent company in 2019, it initiated a move to a cloud-based information network. The company also decided to bring together supply planning, sales and operations planning (S&OP), and demand planning in an environment that would give all employees instant access to a single source of critical supply chain data. Godiva Japan chose Anaplan for this project. “The decisive factor was the ability to oversee the entire supply chain by incorporating data that had been entered manually by each supervisor,” explains Tsuyoshi Tachibana, Godiva Japan’s IT Section Manager, Supply Chain/IT and Product Operations Department.
The Anaplan solution gets most of its data — including all-important product master data — directly from the ERP system via Anaplan Connect. Other data, including “best-before” dates vital to monitor product freshness, are also brought into Anaplan and reflected in production, sales, and inventory forecasts.
Moving forward with greater efficiency
The new solution is delivering a better supply chain process with impressive time savings. Godiva Japan estimates saving 300 hours annually on S&OP reporting, which used to take three days each month for two people. Secondary processing tasks for S&OP data are automatic in Anaplan, saving more than 1,400 hours per year. Compiling retained stock data formerly took three people one full day, but now it is completed “in an instant.”
“The solution has not only saved on labor,” notes Shinya Kushiyama, Godiva Japan’s Director, Supply Chain/ IT and Product Operations. “We have sped up decision-making about supply planning with Anaplan, helping us prevent lost sales opportunities and excess stock.”
And the Godiva Japan team plans to do much more. With two phases of the overall project — supply planning and S&OP — complete, the company is now moving demand planning into Anaplan. It is also leveraging Anaplan to communicate with its supply network.
“By using Anaplan to place orders with the Belgian factory and our suppliers, and integrating it with our finance system, we will make our supply chain management even more efficient going forward,” Kushiyama explains.
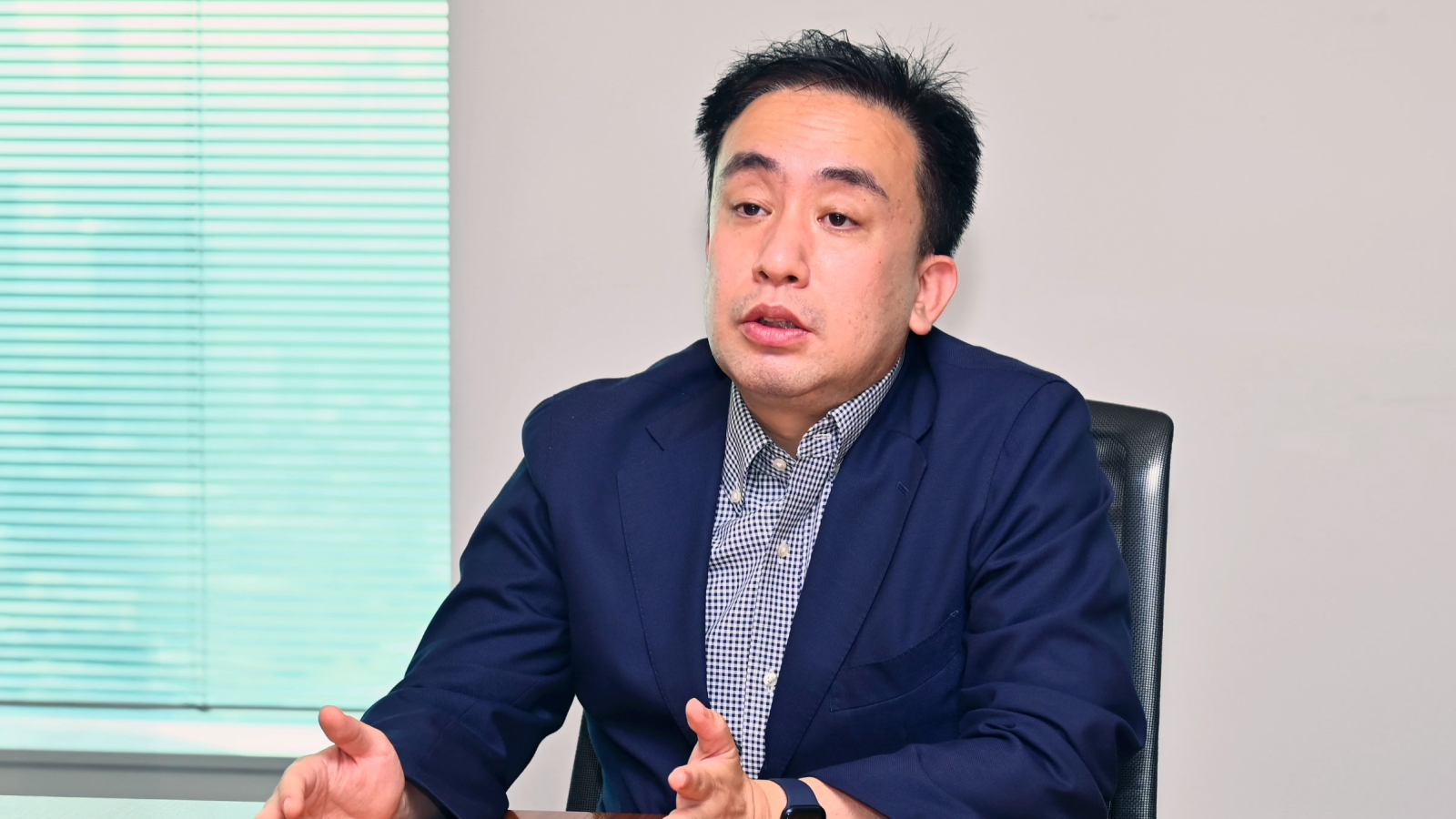
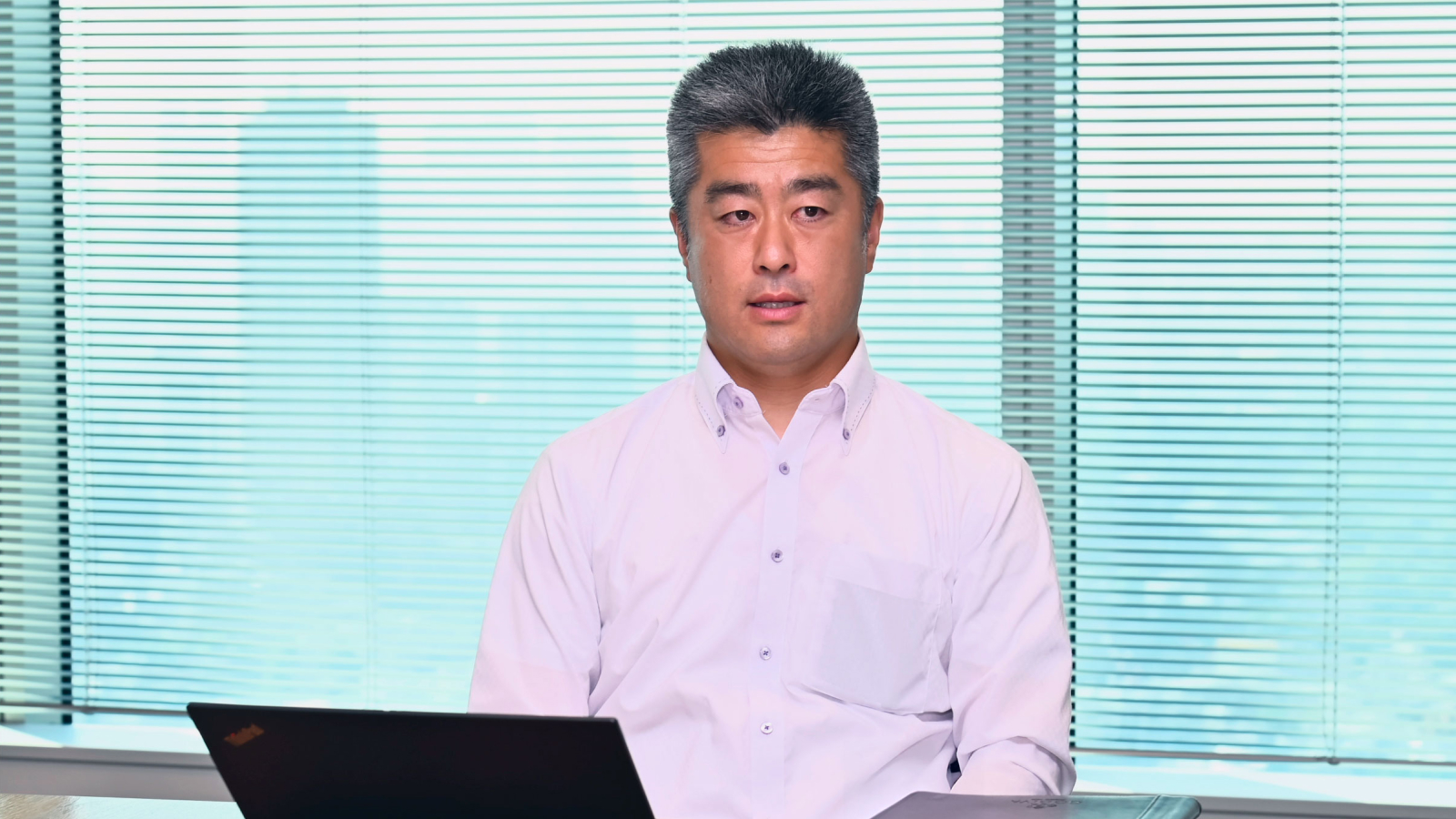